Jietron based on model predictive control algorithm
For different industries and businesses, provide product types in different industries
JETRON based on model predictive control algorithm
Zhuhai JETRON Huazi Technology Co., Ltd. was jointly established by Jie Chuang Technology and Tsinghua University to jointly develop industrial intelligent control software APC (Jie Chuang based model predictive control algorithm), which is widely used in petrochemical, coal chemical, non-ferrous metals, building materials, etc. industry. Jietron's model predictive control algorithm is an indispensable control technology for the optimal operation of the process industry. It can effectively enhance the anti-interference ability and process constraint processing ability of plant production, improve the stability of plant operation, and reduce production fluctuations and the intensity of human intervention. , through the realization of "card edge operation" to fully excavate the process and equipment capabilities of the device, thereby helping customers to obtain maximum economic benefits.
Feature
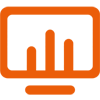
Nonlinear Predictive Control Technology
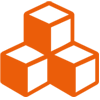
Modeling mechanism that can adapt to the changeable production environment (expansion, transformation)
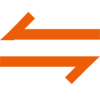
Online Model Switching Technology
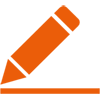
Technology that enables online modification and tuning of controller model parameters
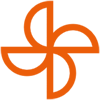
Dynamic Soft Sensing Technology
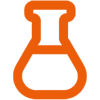
Soft sensing method that can adapt to changing operating conditions (such as raw material properties, large changes in load)
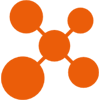
Integrate advanced control technologies such as process mechanism, intelligent control technology, expert operation knowledge, multi-variable predictive control technology and online optimization technology into one “intelligent” advanced control technology for a class of devices
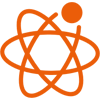
An overall scheduling optimization solution based on the integration of advanced control, online device optimization, raw material blending and scheduling optimization, and product blending optimization
Fundamental
Scroll optimization
★ Calculate the optimal control sequence once in each sampling period, and calculate it again in the next sampling period, and perform rolling execution over and over again, taking into account various uncertainties in the actual control process
★ The error of the model and the disturbance of the system are corrected by feedback through the measured value of the controlled variable, so that the system can reach the actual optimum.
Model estimation
★ Use the model to estimate the motion and error of the controlled object in the future, and use it as the basis for determining the current control effect
★ Adapt the control strategy to the storage, causality and hysteresis of the controlled object, and obtain a better control effect
Feedback correction
★ Use measurable information to correct the estimated value at each sampling time to suppress errors caused by model mismatch and interference
★ Using the revised estimated value as the basis for calculating the optimal control, the robustness of the control system is significantly improved
Related cases
Contact Us
Building 6, Ningxing Jiali Plaza, No. 185 Mingxin Road, Yinzhou District, Ningbo City
Tel:( 86-574 ) 87861201
Fax:( 86-574 ) 87861200
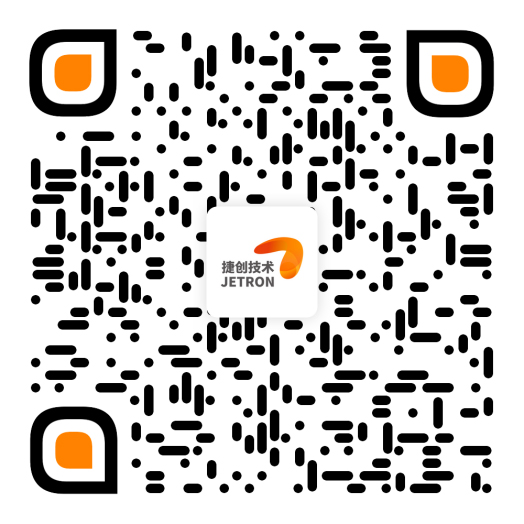
Official Account
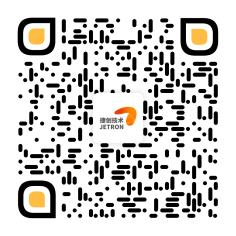
WeChat Channel
© 2021 JETRON Powered by www.300.cn SEO
