Industry Capability
According to the business characteristics of various industries, we create personalized industry solutions and provide users with one-stop products and services.
Industry Capability
Related cases
Metallurgy and Nonferrous Metals
Blast furnace ironmaking:
-
The iron-containing raw materials (sinter, pellets or iron ore), fuels (coke, pulverized coal, etc.) and other auxiliary raw materials (limestone, dolomite, manganese ore, etc.) are charged into the blast furnace in a certain proportion
-
And the hot air is blown into the blast furnace from the hot blast furnace to help the coke burn.
-
Raw materials and fuels decrease with the progress of furnace smelting and other processes
-
In the process of charge falling and gas rising, heat transfer, reduction, melting, and decarbonization occur successively, and pig iron is formed.
-
The impurities in the iron ore raw material are combined with the flux added to the furnace to form slag
-
The molten iron at the bottom of the furnace is intermittently released into the molten iron tank and sent to the steelmaking plant
-
At the same time, two by-products of blast furnace gas and slag are produced. After water quenching, blast furnace slag is all used as raw material for cement production.
Blast furnace ironmaking process and principle
The essence of the ironmaking process:
The process of reducing iron from its natural form, iron-containing compounds such as ore.
Ironmaking methodThere are mainly blast furnace method, direct reduction method, smelting reduction method, etc. The principle is that ore obtains reduced pig iron through physicochemical reaction in a specific atmosphere (reducing substances CO, H2, C; suitable temperature, etc.). Except for a small part of pig iron used for casting, most of it is used as raw material for steelmaking.
Blast furnace ironmaking is the main method of modern ironmaking and an important link in iron and steel production.
This method was developed and improved from the ancient shaft furnace ironmaking. Although many countries in the world have researched and developed many new ironmaking methods, due to the good technical and economic indicators of blast furnace ironmaking, simple process, large production volume, high labor productivity and low energy consumption, the iron produced by this method still accounts for the total iron production in the world. more than 95%.
- During blast furnace production, iron ore, coke, and slag-making flux (limestone) are charged from the top of the furnace
- Blow in preheated air from tuyere located in the lower part of the furnace along the circumference of the furnace
- At high temperature, the carbon in the coke (some blast furnaces also inject auxiliary fuels such as pulverized coal, heavy oil, natural gas, etc.) and the oxygen in the air are combusted to generate carbon monoxide and hydrogen, and the iron ore is removed during the rising process in the furnace. oxygen, which reduces to iron
- The smelted molten iron is released from the iron mouth
- Unreduced impurities in iron ore combine with fluxes such as limestone to form slag, which is discharged from the slag port
- The gas produced is exported from the top of the furnace
- After dust removal, it can be used as fuel for hot blast stove, heating furnace, coke oven, boiler, etc.
The main components of the blast furnace :
1.Blast furnace shell:
Welded steel plate shells are widely used in modern blast furnaces, and only a few of the smallest earth blast furnaces have brick shells reinforced with steel hoops. The function of the furnace shell is to fix the cooling equipment, to ensure that the masonry of the blast furnace is firm, to seal the furnace body, and some also bear the load on the top of the furnace. In addition to bearing huge gravity, the furnace shell also bears thermal stress and internal gas pressure, and sometimes resists the sudden impact of material collapse, material blocking or even possible gas explosion, so it must have sufficient strength. The outer dimensions of the furnace shell should be adapted to the inner shape of the blast furnace, the thickness of each part of the furnace body, and the structure of the cooling equipment.
2. Furnace throat:
The uppermost part of the blast furnace body is cylindrical. The furnace throat is not only the charging port of the charge, but also the outlet of the gas. It controls and regulates the upper distribution of charge and gas. The diameter of the furnace throat should be proportional to the diameter of the hearth, the diameter of the furnace waist and the diameter of the large bell. The height of the furnace throat should allow more than one batch of materials to be loaded, so as to control the distribution of the furnace materials and gas flow.
3. Furnace body:
The main area of indirect reduction of iron ore in blast furnace is truncated cone for short, and it gradually expands from top to bottom, so that the charge will not form a material arch after volume expansion when it is heated, and reduce the descending resistance of the charge. The size of the furnace body angle has a great influence on the fall of the charge and the distribution of the gas flow.
4. Furnace waist:
The part with the largest diameter of the blast furnace. It enables a reasonable transition between the shaft and the belly. Since slag is formed at the furnace waist, and the viscous initial slag will deteriorate the gas permeability of the charge, in order to reduce the resistance of the gas flow, the diameter of the furnace waist can be appropriately enlarged when the amount of slag is large, but it is still necessary to make it and other The size of the part should be kept in an appropriate proportion, and the upper limit of the ratio is appropriate. The height of the furnace waist has little influence on the blast furnace smelting process, and generally only changes in a small range.
5. Hearth:
The main section of blast furnace melting and slagging is in the shape of an inverted truncated cone. In order to adapt to the characteristics of the volume shrinkage of the charge after melting, its diameter is gradually reduced from top to bottom to form a certain belly angle. The existence of the belly keeps the combustion zone in a suitable position, which is conducive to the uniform distribution of airflow. The height of the belly depends on the volume of the blast furnace, but it cannot be too high or too low, generally 3.0 to 3.6 m. The belly angle is generally 79 to 82; if it is too large, it is not conducive to the distribution of gas flow; if it is too small, it is not conducive to the forward flow of the charge.
6. Hearth:
The blast furnace fuel combustion, slag-iron reaction, storage and discharge area is cylindrical. The tap hole, slag outlet and tuyere are all located in the hearth, so it is also the most severe part of the physical and chemical erosion of high temperature gas and slag iron. important influence.
7. Bottom of the furnace:
The masonry at the bottom of the blast furnace must not only withstand the static pressure of the charge, slag liquid and molten iron, but also be subjected to high temperature, mechanical and chemical erosion of 1400-4600 ° C, and the degree of erosion determines the lifetime of the blast furnace. Only when the surface temperature of the masonry is lowered to the solidification temperature of the slag and iron it contacts, and the slag skin (or iron shell) is formed on the surface, can it be prevented from further erosion, so the bottom of the furnace must be cooled. Usually air-cooled or water-cooled. At present, most of the large and medium-sized blast furnaces in our country use full carbon brick bottoms or a comprehensive bottom of carbon bricks and high alumina bricks, which greatly improves the heat dissipation capacity of the bottom.
8. Furnace base:
Its function is to transfer the concentrated weight to the stratum evenly according to the bearing capacity of the stratum, so its shape expands downward. The total weight of the blast furnace and the furnace base is often 10 to 18 times the volume of the blast furnace (tons). The furnace foundation shall not have uneven subsidence, and generally the inclination value of the furnace foundation shall not be greater than 0.1% to 0.5%. The blast furnace foundation should have sufficient strength and heat resistance to prevent cracks under various stresses. The furnace base is often made into a circle or a polygon to reduce the uneven distribution of thermal stress.
9. Furnace lining:
The blast furnace lining constitutes the working space of the blast furnace and serves to reduce blast furnace heat loss and protect the furnace shell and other metal structures from thermal stress and chemical attack. The furnace lining is made of refractory materials that can resist high temperature. The damage of the furnace lining is affected by various factors. The working conditions of each part are different, and the damage mechanism is also different. Therefore, different refractory materials must be selected according to factors such as location, cooling and blast furnace operation.
10. Furnace throat guard:
Under the frequent impact of the charge and the scouring of the high-temperature gas flow, the working conditions of the throat of the furnace are very bad. It is a prerequisite for the upper part of the blast furnace to maintain its cylindrical shape from being damaged. For this purpose, a protective plate (steel brick) is installed at the throat of the furnace. The throat protection plate of the small blast furnace can be made of cast iron into an open box shape; the throat protection plate of the large blast furnace is made of cast steel with a thickness of 100-150mm. Furnace throat guards are mainly in block, strip and variable diameter forms. The variable diameter furnace throat guard also plays a role in regulating the distribution of the charge and gas flow.
11. The blast furnace disintegration:
In order to properly handle the complex phenomena that often occur in blast furnace smelting, it is necessary to understand the furnace conditions. After shutting down the blast furnace, water injection cooling or nitrogen filling cooling while maintaining the original production state of the blast furnace as much as possible, the detailed disintegration investigation from the charge of the furnace throat to the iron deposit at the bottom of the furnace is called blast furnace disintegration investigation. Although it cannot fully understand the dynamic situation of blast furnace production, it is of great reference value for understanding blast furnace process and strengthening blast furnace smelting.
12. Blast furnace cooling device:
The internal temperature of the blast furnace lining is as high as 1400 ℃, and the general refractory bricks are softened and deformed. The blast furnace cooling device is set up to prolong the life of the brick lining, which is used to transfer the heat in the furnace lining and condense the slag on the furnace lining into a protective slag skin at the lower part of the blast furnace. According to different structures, blast furnace cooling equipment can be roughly divided into For: external water spray cooling, tuyere slag cooling, cooling wall and cooling water tank and air-cooled (water-cooled) furnace bottom and other devices.
13. Blast furnace ash:
Also called furnace dust, it is the charge powder carried by the blast furnace gas. The quantity is not only related to the blast furnace smelting strength and furnace top pressure, but also has a great relationship with the properties of the charge. The more powder of the charge, the larger the amount of dust brought out. At present, about 10-100kg of blast furnace ash is produced per ton of iron smelted. Blast furnace ash usually contains about 40% iron, and contains more carbon and basic oxides; its main components are coke powder and mineral powder. Adding part of blast furnace ash to the sintered material can save flux and reduce fuel consumption.
14. Blast furnace dust collector:
Equipment used to collect dust contained in blast furnace gas. Dust collectors for blast furnaces include gravity dust collectors and centrifugal dust collectors.
Blast Furnace Automation Control System
Blast furnace automation control is like the control nervous system of blast furnace. In order to ensure safe, reliable and stable operation of blast furnace, the reliable and stable operation of blast furnace basic automation system must be ensured. The basic automation communication network of the blast furnace and the PLC system are redundant. The connection between the PLC and the HMI monitoring screen through the fault-tolerant server can ensure the reliable and stable operation of the entire system. The network structure of the blast furnace basic automation system and the configuration and control of each system are described in detail below.
The network structure of the blast furnace basic automation control system has a total of 3 kinds of networks. The network of PLC, monitoring screen and secondary system adopts standard Ethernet, which is easy to connect with the factory-level network and easy to maintain. The main process adopts PLC control system using ControlNet network, the network data exchange speed is fixed at 5M, and has a high data exchange speed, which can ensure the real-time requirements of data acquisition of the control system. The probe encoder on the furnace top adopts the DeviceNet network, and the maximum speed of the network data exchange is 500K. The actual speed of data exchange is determined according to the network length and the actual situation of the site. Because the amount of data exchange with the encoder is limited, and the real-time data exchange rate is limited. The performance requirements are not very high, and it can meet the control requirements of the bellless furnace top.
The electrical and instrumentation control system of the main process adopts Rockwell's ControlLogix control system, a total of 7 sets, including the under-trough and charging system, furnace top and body system, hot blast furnace and casting yard system, injection and pulverizing The CPU of the system and water treatment system adopts a redundant configuration, the gas purification system and the water slag system are controlled by a single CPU, the CPU and the HMI fault-tolerant server use a redundant Ethernet network, and the communication between the CPU and I/O modules adopts a redundant ControlNet network. At the same time, the PLC power supply adopts redundant power supply.
1) Under-trough weighing system: including ore and coke weighing control, belt transportation, intermediate hopper charging and weighing, weighing correction, coke moisture correction, material empty control of weighing hopper, material full control, etc.
2) Feeding belt system: discharge control of ore, small coke weighing hopper and coke intermediate hopper, operation control of feeding belt conveyor and raw material tracking control, etc.
3) Furnace top system: furnace top charging control, furnace top equipment timing control, furnace top distribution control, etc.
4) Hot blast stove and waste heat recovery system: air supply sequence control and furnace change control of the three hot blast stoves, waste heat recovery system control, combustion control, air supply temperature control, etc.
5) Gas purification system: Gravity dust removal equipment control, bag dust removal equipment control, ash discharge sequence control, ash powder back-blowing sequence control, furnace top pressure control, etc.
6) Pulverized coal injection system: control of the injection equipment of the pulverized coal injection system, etc.
7) Water treatment system: interlock control of water treatment equipment, etc.
8) Blast furnace body system: water temperature, water pressure and water flow measurement of cooling water system, furnace top sprinkler control, furnace body static pressure measurement, temperature measurement and alarm of various cooling equipment and refractory materials in the body, control of the hydraulic station in the tapping yard, and tapping Field dust removal valve, dust removal fan, motor control, etc.
The system network diagram is shown in the figure:
Contact Us
Building 6, Ningxing Jiali Plaza, No. 185 Mingxin Road, Yinzhou District, Ningbo City
Tel:( 86-574 ) 87861201
Fax:( 86-574 ) 87861200
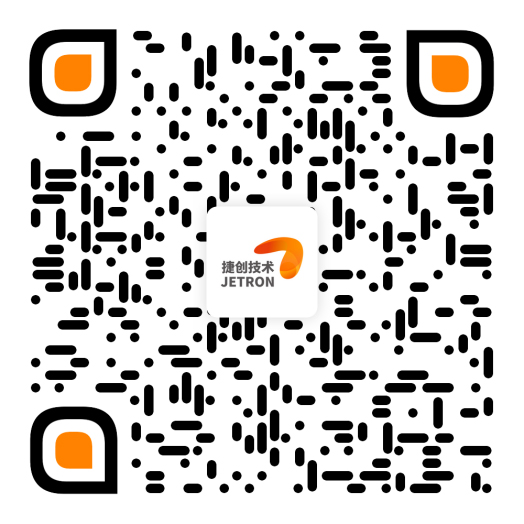
Official Account
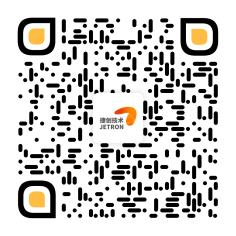
WeChat Channel
© 2021 JETRON Powered by www.300.cn SEO
