Industry Capability
According to the business characteristics of various industries, we create personalized industry solutions and provide users with one-stop products and services.
Industry Capability
Related cases
Building materials industry
1、Cement production line process
1.1、Process Description
Generally speaking, the cement industry produces Portland cement, a fine, usually gray powder composed of calcium (from limestone), silicates, aluminates (clay), and iron acid composition. In a Portland cement factory, the main process of the cement production process is that the raw materials are crushed and ground to make raw meal, and then the raw meal is sent to a high-temperature kiln to calcine clinker with fuel, and finally the clinker is mixed with clinker. A suitable amount of gypsum is mixed and ground into cement, which requires multiple processes such as mining, raw material crushing, clay drying, raw meal grinding, clinker calcination, clinker cooling, cement grinding and finished product packaging.
In short, its production process can be summarized as "three mills and one kiln", which can be divided into four steps:
1、 Preparation of raw meal: Crushing the calcareous raw materials, clay raw materials and a small amount of calibrated raw materials according to a certain proportion, grinding them finely and preparing them into a suitable raw meal with uniform quality and quality;
2、 Preparation of medium powder: The coal required for the calcination of cement raw meal must be prepared into medium powder to provide the particle size required for the combustion of the medium powder, so as to facilitate full combustion and obtain sufficient combustion reaction capacity;
3、 Clinker calcination: The diameter of the clinker spherical agglomerates must be in the range of 0.32-5.0cm, which are produced in the chemical reaction between the raw materials. The raw meal is calcined in a cement kiln until it is partially melted and Portland cement clinker is obtained, and stored in a clinker silo;
4、Cement grinding and leaving factory: the clinker is added with appropriate amount of gypsum, admixture or additives to grind it into cement, and package it for delivery. The grinding process takes place in a closed system equipped with an air separator to separate the cement particles by size, and material that is not fully ground is re-routed through the system.
1.2Process system overview
1.2.1Crushing and pre-homogenizing
1、broken
In the process of cement production, most of the raw materials are crushed, such as limestone, clay, iron ore and coal. Limestone is the most used raw material for cement production. After mining, the particle size is large and the hardness is high. Therefore, the crushing of limestone plays an important role in the crushing of materials in cement plants.
2、Raw material pre-homogenization
The pre-homogenization technology is to use the scientific stacking and reclaiming technology to realize the initial homogenization of the raw materials in the process of storage and retrieval of raw materials, so that the raw material yard has the functions of storage and homogenization at the same time. The pre-homogenization of raw materials is controlled by process control, which is more convenient for homogenization and storage of raw materials. AB's FactoryTalk SE host computer software is used to carry out data communication through the Hirschmann RS20 switch to realize remote control and monitoring.
1.2.2Raw meal preparation
In the cement production process, at least 3 tons of materials (including various raw materials, fuels, clinkers, mixtures, and gypsum) must be ground for every 1 ton of Portland cement produced. Power accounts for more than 60% of the power of the whole plant, of which raw meal grinding accounts for more than 30%, coal grinding accounts for about 3%, and cement grinding accounts for about 40%. Therefore, reasonable selection of grinding equipment and process flow, optimization of process parameters, correct operation, and control of operation system are of great significance to ensuring product quality and reducing energy consumption.
1.2.3 Raw Meal Homogenization
In the production process of the new dry process cement, the stability of the raw meal composition in the cellar is the premise of stabilizing the thermal system of clinker firing, and the raw meal homogenization system plays the last gate of stabilizing the raw meal composition in the cellar. The Rockwell controller was used to optimize the PID temperature, and FactoryTalk SE was used to optimize the data parameters.
1.2.4 Preheat decomposition
The preheating and partial decomposition of the raw meal are completed by the preheater, which replaces some of the functions of the rotary kiln, so as to shorten the length of the return kiln, and at the same time, the kiln can carry out the gas-material heat exchange process in a stacked state, and move it to the suspended state in the preheater. It is carried out under the kiln, so that the raw meal can be fully mixed with the hot gas discharged from the kiln, which increases the contact area of the gas and the material, the heat transfer speed is fast, and the heat exchange efficiency is high, so as to improve the production efficiency of the kiln system and reduce the heat consumption of clinker firing. Purpose.
1、Material dispersion
80% of the heat exchange is carried out in the inlet pipe. The raw material fed into the preheater pipeline is impacted by the high-speed updraft, and the material turns upward and moves with the airflow, and is dispersed at the same time.
2、Gas-solid separation
When the airflow carries the powder into the cyclone, it is forced to rotate in the annular space between the cyclone barrel and the inner barrel (exhaust pipe), and moves downward while rotating, from the barrel to the cone , which can extend all the way to the end of the cone, and then turns upward and rotates upward, and is discharged by the exhaust pipe.
3、Pre-decomposition
The emergence of pre-decomposition technology is a technological leap in cement calcination process. It is to add a decomposition furnace between the preheater and the rotary kiln, use the kiln tail to rise the flue, and set up a fuel injection device to make the exothermic process of fuel combustion and the endothermic process of carbonate decomposition of raw meal. The furnace is rapidly carried out in a suspended state or a fluidized state, so that the decomposition rate of the raw meal entering the kiln can be increased to more than 90%. The carbonate decomposition task originally carried out in the rotary kiln is moved to the decomposition furnace; most of the fuel is added from the decomposition furnace, and a small part is added from the kiln head, which reduces the heat load of the calcination zone in the kiln and prolongs the lining of the kiln. The life of the material is long, which is beneficial to the large-scale production; because the fuel and the raw material are mixed evenly, the combustion heat of the fuel is transferred to the material in time, so that the combustion, heat exchange and carbonate decomposition processes are optimized. Therefore, it has a series of excellent performance and characteristics such as high quality, high efficiency and low consumption.
1.2.5 Firing of cement clinker
After the raw meal is preheated and pre-decomposed in the cyclone preheater, the next process is to enter the rotary kiln for clinker firing. In the rotary kiln, the carbonate is further rapidly decomposed and a series of solid-phase reactions occur to generate minerals in the cement clinker. As the temperature of the material increases, the minerals will turn into a liquid phase, and the dissolved in the liquid phase will react with and produce a large amount of (clinker). After the clinker is fired, the temperature begins to decrease. Finally, the cement clinker cooler cools the high temperature clinker discharged from the rotary kiln to the temperature that the downstream conveying, storage and cement mill can bear, and at the same time recovers the sensible heat of the high temperature clinker to improve the thermal efficiency and clinker quality of the system.
1.2.6 Powder preparation
1.2.7 Clinker preparation
1.2.8 Cement grinding
Cement grinding is the final process of cement manufacturing, and it is also the process that consumes the most electricity. Its main function is to grind cement clinker (and gelling agent, performance adjusting material, etc.) to a suitable particle size (represented by fineness, specific surface area, etc.) to form a certain particle gradation and increase its hydration area. Accelerates the hydration speed and meets the requirements of cement paste coagulation and hardening.
In limestone crushing electrical room, limestone pre-homogenization electrical room, raw material grinding and waste gas treatment, raw material grinding electrical room, clinker conveying, firing kiln head, kiln head electrical room, coal powder preparation and metering transportation, coal grinding electrical room , Kiln tail electrical room. The fans, belt conveyors, plate feeders, etc. in each electrical room are driven by Rockwell PF753 series frequency converters, of which the plate feeder and belt conveyor are of heavy-duty type, with dual-motor master-slave control through Hirschmann RS20 switch communication forms a ring network, the inverter is controlled by magnetic flux vector, and the built-in DviesLogix logic control function is a dual motor to achieve torque synchronization function. The hoist adopts Rockwell SMC-Flex soft start, with optional soft start of kick start, current limit start, double ramp start, full pressure start, preset low speed, linear acceleration of sudden jump start, soft stop function, Optional communication network card, Ethernet card using 20COMME. The rotary kiln adopts Rockwell PowerFlexDC DC drive, and the armature excitation is integrated. The liquid crystal display panel is easy to operate, and a variety of network communications can be used with the inverter soft-start communication card. It has a high-performance control mode, which can display segment speed operation, the current of 690V voltage level can reach 1500A, and the dual DC drive synchronous master-slave control. The Hoffman MI9 cabinet used in the control cabinet of each electrical room has a protection grade of IP55, which can prevent dust in places with more dust. In the process of merging cabinets, the cabinet components are used, so that the protection level of the cabinet is not lowered. Better for applications in individual electrical rooms.
2.3 System Components
★For PA bus instruments and complete sets of equipment with DP, we use DA's Modbus communication gateway, and connect these devices to industrial switches through Ethernet, and then to the control system through OPC. A communication gateway has 2 RS485 interfaces, each interface can carry up to 32 stations, the communication transmission rate: 1200 bit/s~115.2Kbit/s.
★Using FactoryTalk SE software, using server/clinet structure, server and communication are configured in pairs, two servers are backup for each other, if any one server fails, the other server can be switched without disturbance.
★It adopts imported industrial-grade managed Hirschman switches, supports ring network technology, and the self-recovery time of ring network failure is less than 20ms.
★Using the WEB publishing software of the FactoryTalk platform for network publishing, you can see the content of the upper computer screen in the IE browser, which meets the BS architecture.
★Using Rockwell Industrial Data Center IDC to establish an industrial private cloud Using the current mainstream industrial data center virtualization technology, each system server in the production area (including MES server, SCADA management server, historical database server, real-time database server, WEB publishing Server, video server, security server, etc.), operator station, engineer station systems are centralized on the private cloud server of the group or factory, and thin clients are placed on the traditional system operator station. Subverting the traditional structure, it not only maintains the original server architecture to the greatest extent, but also uses private cloud technology to enhance server performance and reliability, prolong the system life cycle, and protect the user's investment.
Contact Us
Building 6, Ningxing Jiali Plaza, No. 185 Mingxin Road, Yinzhou District, Ningbo City
Tel:( 86-574 ) 87861201
Fax:( 86-574 ) 87861200
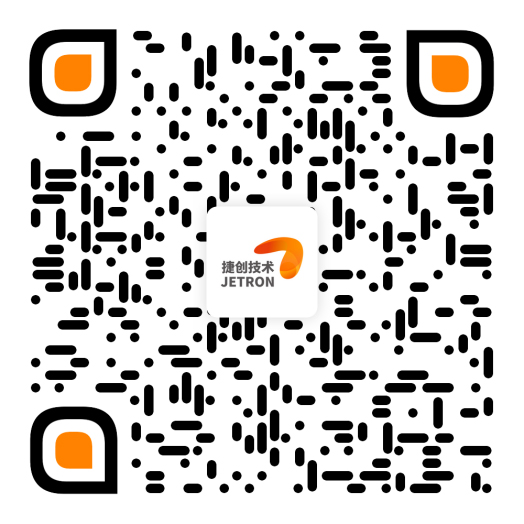
Official Account
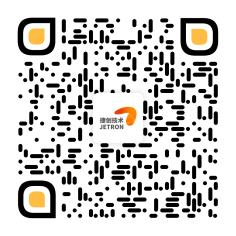
WeChat Channel
© 2021 JETRON Powered by www.300.cn SEO
