Industry Capability
According to the business characteristics of various industries, we create personalized industry solutions and provide users with one-stop products and services.
Industry Capability
Related cases
Power Industry
1、Monitoring system structure
The computer monitoring system of the hydropower station is functionally divided into: the power station control layer and the local control layer.
(1)power station control layer
The power station control layer is composed of the relevant main control level monitoring equipment in the power station computer room and the central control relay protection room. The main equipment includes the main computer of the power station, operator workstation, operator console, training platform, engineer/training workstation, communication workstation, voice alarm and ON-CALL workstation, satellite synchronous clock system, printer and CD recorder, UPS, etc.
(2) local control layer
The local control unit level consists of seven local control units, and each LCU shall be intelligent and have programmable capabilities. LCU uses AB's ControlLogix's 1756 series products for hardware redundancy, supports hot-swap with point, runs in master/hot standby mode, and realizes redundant switching through Rockwell's redundant control module (1756-RM2) without additional programming. , the bottom adopts Ethernet ring network (DLR) for network redundancy. Use 1756-EN2TR for ring or star redundancy with the host computer.
(3)Operator workstation (2 sets)
The computer is located in the computer room of the power station workshop, and adopts a double-machine fully redundant configuration. Under normal conditions, one is working and the other is hot standby. If the working computer fails, the standby computer will take over and automatically complete the non-disturbance switching between the two machines. The software adopts the Server version of FactoryTalk View SE, and uses two server software for backup and switching. The backup and switching are all realized by the Server itself. The central control room is equipped with a set of UPS power supply with a capacity of not less than 3kVA. Featuring the Alpha Continuity 3KVA online UPS series, it is designed to perform rack/tower conversion using a rotating LCD panel, making it easy to integrate into a variety of applications and networks.
(4)Server Industry Private Cloud
Using the current mainstream industrial data center virtualization technology, each system server (including MES server, SCADA management server, historical database server, real-time database server, WEB publishing server, video server, security server, etc.) in the production area, operator station , The system of the engineer station is concentrated on the private cloud server of the group or factory, and the thin client is placed on the traditional system operator's position. Subverting the traditional structure, it not only maintains the original server architecture to the greatest extent, but also uses private cloud technology to enhance server performance and reliability, prolong the system life cycle, and protect the user's investment.
2、Network mode
◆The local area network must conform to the international standard IEE802.3u and the TCP/IP stipulation commonly used by the industry.
◆The local area network adopts a 100M fiber single ring network structure, and the power station control level equipment and the local control unit equipment are directly connected to the local area network.
◆The network equipment of the main station adopts industrial-grade Gigabit Ethernet ring network switches, and the local LCU network equipment adopts industrial-grade 100MHz Hertzmann RS series switches. Panduit Category 5 cables are used between the main station switch and each workstation.
Industrial Ethernet switches are Hirschmann RS series specially designed for harsh industrial environments. Its materials, components and installation methods are strictly designed and manufactured in accordance with industrial grades. Industrial indicators such as interference, vibration, shock, industrial temperature, etc., to ensure high reliability of the network. The equipment adopts a fanless design, supports 12~48VDC dual power supply redundancy, and has the function of reverse polarity protection of the power supply. Its performance index far exceeds that of general commercial network products. At the same time, the switch adopts standard industrial guide rail and rack-mounted installation, which is convenient for equipment setting in the industrial field.
The device supports redundant dual DC power input, which can automatically switch in case of failure of the main power supply system. And support the reverse polarity protection function of the power supply, when the positive and negative poles of the power supply are reversed, not only will the equipment not be burned, but it can continue to work normally, so it can well ensure the reliability of the network communication system and the safety of the equipment .
The structure of the whole machine is designed in strict accordance with the relevant electromagnetic compatibility design specifications, which ensures that the system has good anti-static interference, anti-radio frequency interference, anti-electric burst interference, anti-lightning surge interference, anti-electric instantaneous drop interference and anti-radio frequency conduction interference. Ability
3、Clock system
The clock synchronization system adopts the special module of AB, which conforms to the IEEE1588 PTP time synchronization requirements.
4、Control layer
The working power of each remote I/O is provided by its corresponding LCU respectively.
◆Unit local control unit (LCU1, LCU2, LCU3, LCU4)
The LCU should provide the RS-485 serial interface, the interface using the Modbus (Master and Slave) standard communication protocol, and the Molex for gateway protocol conversion. The module is directly inserted into the AB 1756 rack, and there are standard blocks for programming.
The international standard industrial Ethernet protocol EtherNet/IP is used between the PLC in the LCU and the workstation, and the communication rate reaches 100Mbps. The PLC uses the AB ControlLogix system governor oil pump control circuit and ball valve control circuit to enter the local LCU control of the unit.
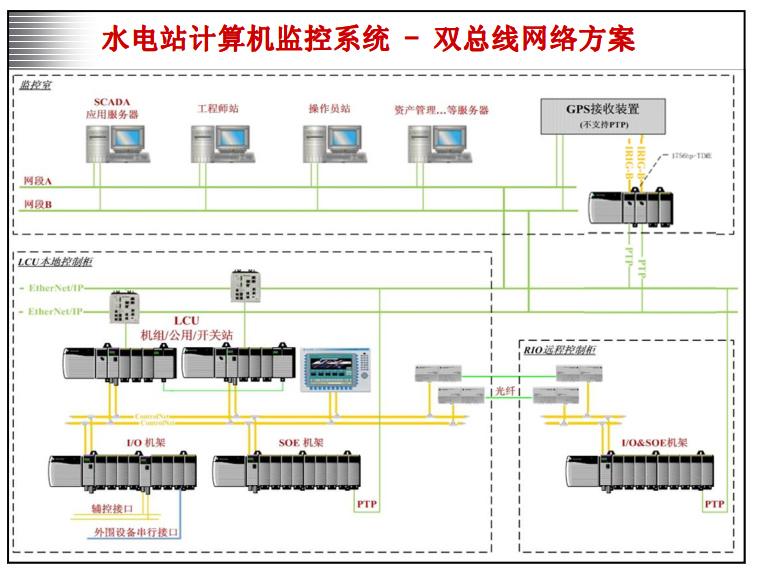
◆ Public booster station local control unit (LCU5)
1 set of switch station local control unit LCU. LCU consists of AB's 1756 series plus PanelView Plus 7 series touch screen.
The international standard industrial Ethernet protocol EtherNet/IP is used between the PLC in the LCU and the workstation, and the communication rate reaches 100Mbps. The control system uses the AB ControlLogix system.
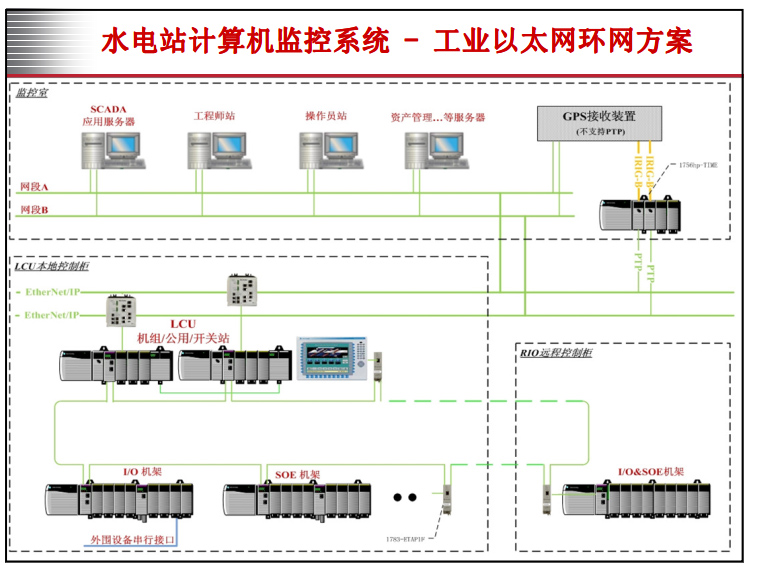
The bottom drive adopts Rockwell PowerFlex753 series inverter, adopts EtherNet/IP communication module with dual Ethernet interface, can realize DLR function (Ethernet ring network), Rockwell drive has a variety of control modes, standard V/ Hz, with full customization, speed sensorless vector control, with auto-tuning, flux vector control, with or without encoder feedback, induction and permanent magnet motor control.
Add industrial firewall Tofino on the bottom controller side. Regardless of the attack or human error anywhere in the network, the defense-in-depth model can effectively limit its impact on the entire network. Multi-layer protection, differentiated protection, and layering for specific threats protection.
Thermal power industry capabilities of the power industry:
Water network PLC control system
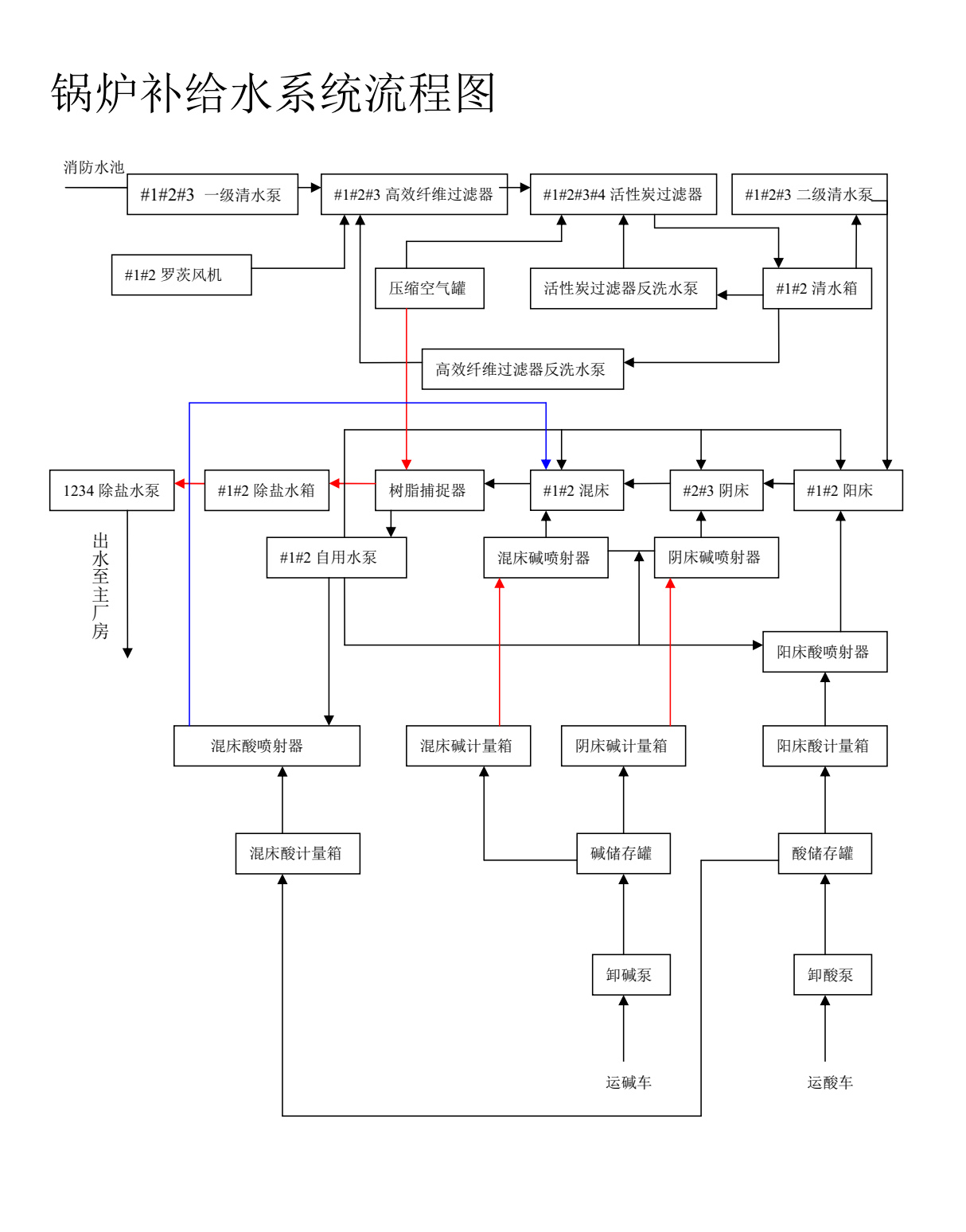
Coal conveying program control PLC system
The coal conveying program control system of the whole plant adopts the hierarchical control structure of control system + network + upper computer and access to the auxiliary system centralized monitoring network. The programmable controller should choose the Rockwell ControlLogix series products with mature operating experience in the power plant, and use the same series of modules to reduce the amount of spare parts and maintenance; all modules can be plugged, including CPU, power module, communication module, I/O module, support non-stop maintenance; output module requires pre-set fault handling function. The PLC device adopts a unified high-speed backplane bus, and the speed of the backplane bus is not less than 80M to ensure consistent system performance. The system is equipped with 2 sets of PLC system CPU with redundant configuration. One set of redundant CPU controls the coal handling control system; the other set of redundant CPU controls the fuel pump room control system. A total of 2 sets of mutually redundant debugging operator stations/engineer stations are set up.
Gray net PLC control system
The plant ash network control system is composed of the fly ash removal control system, the slag removal control system, the fly ash sorting control system, and the electric bag filter control system. The workshop centralized monitoring network realizes the monitoring, operation and control of the above systems and equipment through the upper computer of the whole factory gray network control system or the upper computer operator station of the whole auxiliary workshop centralized monitoring system, and ensures their normal and reliable operation. The programmable controller should choose the Rockwell ControlLogix series products with mature operating experience in the power plant, and use the same series of modules to reduce the amount of spare parts and maintenance;all modules can be plugged, including CPU, power module, communication module, I/O module, support non-stop maintenance; output module requires pre-set fault handling function. The PLC device adopts a unified high-speed backplane bus, and the speed of the backplane bus is not less than 80M to ensure consistent system performance. The system is equipped with 2 sets of redundant configuration PLC system CPU control fly ash system.
The fly ash removal system for each furnace includes the centralized transportation, storage and treatment of the ash hopper of the electric bag filter and the economizer/denitrator. The flow chart is as follows:
The flow chart of the slag removal system is as follows:
The bottom drive adopts Rockwell PowerFlex753 series inverter, adopts EtherNet/IP communication module with dual Ethernet interface, can realize DLR function (Ethernet ring network), Rockwell drive has a variety of control modes, standard V/ Hz, with full customization, speed sensorless vector control, with auto-tuning, flux vector control, with or without encoder feedback, induction and permanent magnet motor control.
The cabinet adopts Hoffman MI9 cabinet, the protection level is IP55, according to the standard GB 4208, which is equivalent to IEC 60529. It has super load-bearing capacity, and the cabinet components can be perfectly combined between cabinets in the same workshop, in the smart grid industry Medium, Hoffman MODO modular double-layer outdoor cabinet, double-wall structure, superior thermal solution, 75% energy saving than ordinary cabinets, made of high-quality stainless steel and aluminum plate, high-strength aluminum alloy frame, good anti-vibration , Anti-earthquake, load and EMC function, protection grade IP55.
Add industrial firewall Tofino on the bottom controller side. Regardless of the attack or human error anywhere in the network, the defense-in-depth model can effectively limit its impact on the entire network. Multi-layer protection, differentiated protection, and layering for specific threats protection.
The topology diagram of the auxiliary network control system of the whole plant is as follows:
Contact Us
Building 6, Ningxing Jiali Plaza, No. 185 Mingxin Road, Yinzhou District, Ningbo City
Tel:( 86-574 ) 87861201
Fax:( 86-574 ) 87861200
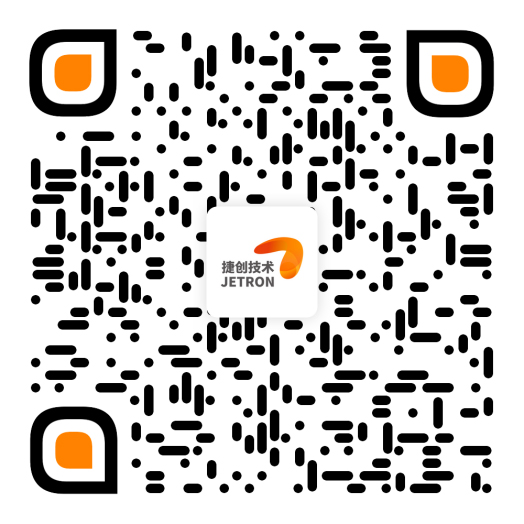
Official Account
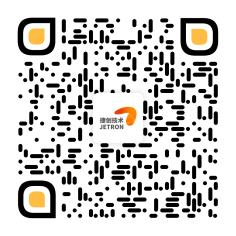
WeChat Channel
© 2021 JETRON Powered by www.300.cn SEO
